How AI is Transforming Fabric Fusing – A Guide for Small Garment Factories and Brands
| Nov, 27 , 24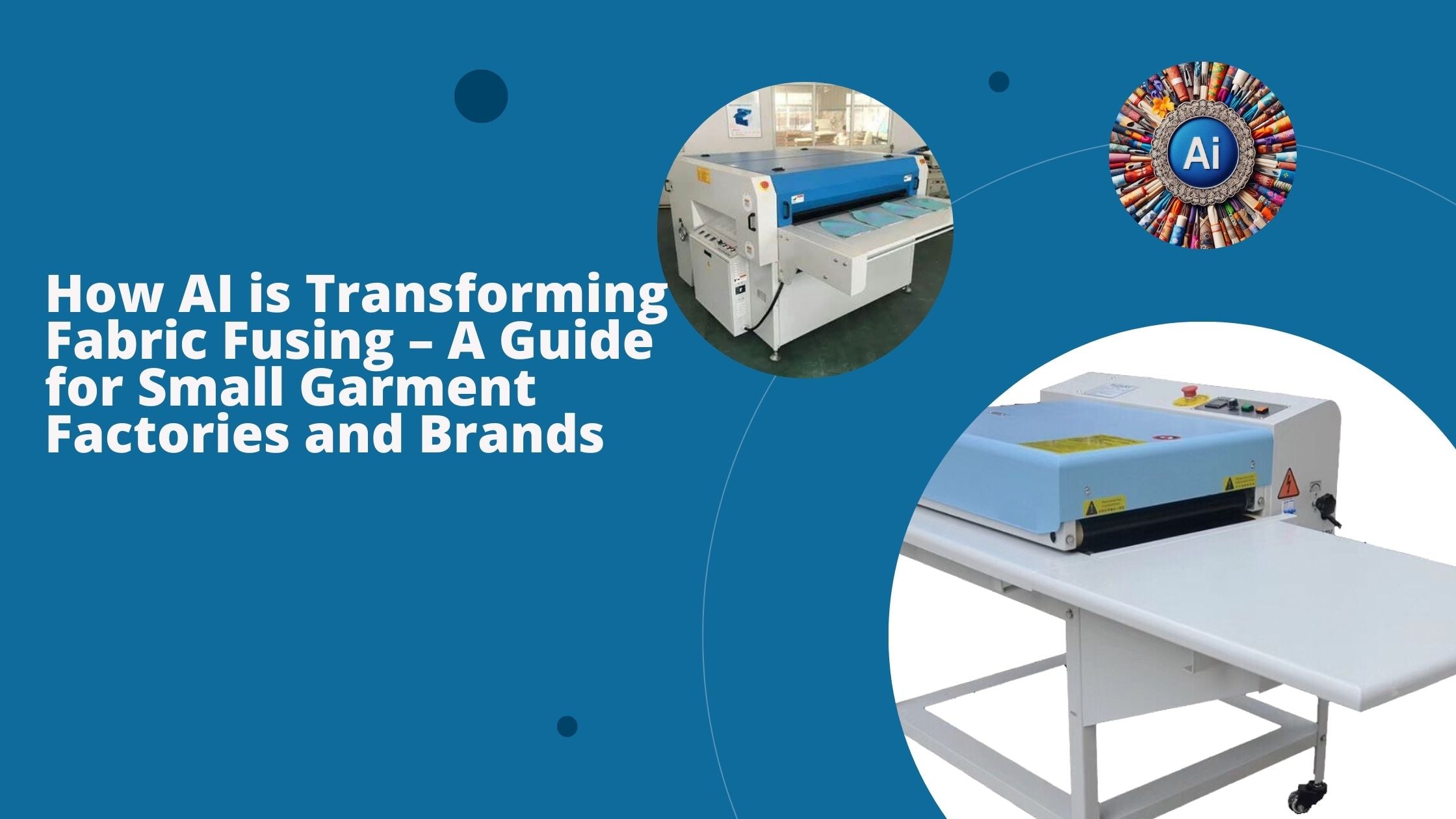
The Role of AI in Modern Fabric Fusing
Fabric fusing is crucial in garment manufacturing, ensuring strength, structure, and shape retention by bonding interlining between fabric layers. From collars to jackets to automotive interiors, fusing plays a vital role in maintaining the durability and appearance of finished products. Traditionally, this process required precise manual control of heat and pressure, but advancements in technology—specifically AI-powered fabric fusing machines—are revolutionizing the process.
AI offers a game-changing opportunity for garment factories by making fusing machines more intelligent, efficient, and capable of real-time adjustments. For small factories and emerging brands, AI integration levels the playing field, enabling them to meet industry standards, reduce defects, and compete with prominent players—all without compromising quality or speed.
This blog will dive into the essentials of fabric fusing, exploring the different techniques and types of machines available. We will discuss how AI enhances fusing operations through automation, predictive maintenance, and error detection. Finally, we will highlight the benefits of AI-powered fabric fusing for small garment businesses, including cost savings, efficiency, and improved product quality. Whether in fashion, automotive, or medical manufacturing, this guide will show how adopting AI can transform your fusing process and help your brand stay competitive. Let us start from the beginning.

What is Fabric Fusing, and Why is It Important?
Fabric fusing is bonding two or more fabric layers by applying an interlining with adhesive resin, using heat and pressure. The primary purpose is to provide structure, strength, and shape retention to garments, ensuring they maintain their form over time. It is used extensively in products like collars, cuffs, and suits to enhance sturdiness while also playing a role in non-apparel sectors, such as automotive upholstery and medical textiles.
How Fabric Fusing Differs from Traditional Sewing Methods
Traditional garment manufacturing often involves sewing interlinings or additional layers into fabric pieces. However, sewing can sometimes create bulky seams and may not provide the even, smooth finish required for certain fabrics or styles. Fabric fusing offers a more seamless and efficient solution.
- It allows a sleek and smooth appearance by eliminating the bulky stitching.
- Time and labor savings as it reduces manual sewing and stitching.
- Better performance for lightweight materials, where stitching could cause puckering or misalignment.
It makes fabric fusing the preferred choice for high-volume production and garments requiring clean, tailored finishes.
The Importance of Consistent, High-Quality Fabric Fusing
Precision is vital in fabric fusing because inconsistencies in heat or pressure can lead to defects, such as fabric deformation or adhesive bleeding through the fabric (strike-through). Proper fusing ensures:
- Durability: The bonded fabrics maintain their integrity, even after multiple washes.
- Aesthetic Appeal: No visible signs of adhesive or wrinkles that could impact the garment's look.
- Shape Retention: Garments, especially those with structured components, maintain their shape over time.
For businesses focused on delivering high-quality products, mastering the fusing process is essential to meet consumer expectations and reduce waste caused by defective items.

Fabric Fusing Machines: A Modern Solution for Garment Manufacturing
How Fabric Fusing Machines Work
Fabric-fusing machines automate the bonding by controlling key variables like heat, pressure, and processing time.
- Preparation: They lay out the fabric and adhesive-coated interlining.
- Preheating: The machine reaches the desired temperature to prevent shrinkage and prepare the adhesive for bonding.
- Bonding: They feed the fabric and interlining into the machine, which applies precise heat and pressure to activate the adhesive.
- Cooling: They set aside the material to cool. It solidifies the adhesive once bonded.
Importance of Precise Control in Fabric Fusing Machines
Maintaining the right temperature, pressure, and timing is essential for avoiding defects like:
- Strike through: When adhesive resin seeps through to the top layer, compromising the appearance.
- Strike Back: When the adhesive spreads to the back layer, affecting texture and durability.
Modern fusing machines incorporate automated controls, ensuring consistent results across production batches. This precision reduces waste, enhances product quality, and allows factories to meet production deadlines more efficiently.
Types of Fabric Fusing Techniques
Reverse Fusing
- How it Works: In reverse fusing, the interlining is placed with the resin-coated side facing upwards and the fabric over it.
- Best Use: This method is ideal for small or intricate fabric pieces like collars or cuffs. It ensures the proper interlining bonds without shifting during the fusing process.
Sandwich Fusing
- How it Works: This technique involves layering fabric, interlining, and another layer or interlining in a sandwich formation. The layers go through continuous fusing machines that apply heat and pressure.
- Best Use: Sandwich fusing is helpful in high-volume multiple layers like thick garments, automotive textiles, or structured apparel.
Double Fusing
- How it Works: Double fusing involves bonding two interlinings with the same fabric. This method requires precise control to ensure that neither layer shifts nor becomes misaligned during bonding.
- Best Use: They employ double fusing for jackets, blazers, and other structured garments needing extra rigidity and strength. It enhances the durability and shape of products where standard fusing might not suffice.

Fabric Fusing Defects and How to Avoid Them
Strike Back: Causes and Impact on Fabric Quality
Strikeback occurs when the adhesive resin from the interlining migrates to the back side of the fabric, resulting in visible stains or changes in texture. This defect is caused by:
- Excessive heat or pressure forces the adhesive to spread beyond the intended layer.
- Incorrect fabric preparation, where the interlining shifts or is misaligned during fusing.
Impact:
Strikeback compromises the durability and aesthetic appeal of the garment. It can stiffen, reduce flexibility, and alter the texture of soft fabrics like cotton or silk.
Solution:
- Maintain precise control over heat and pressure to prevent resin migration.
- Pre-test settings with sample fabrics to avoid over-bonding.
- Use AI-powered machines to monitor temperature and adjust settings to match the specific fabric type.
Strike-through: Causes and Impact on Appearance and Comfort
It occurs when the adhesive penetrates the interlining fabric, appearing on the top surface. This defect is usually caused by:
- Overheating or excessive pressure pushes the adhesive through all fabric layers.
- Using incompatible interlining that cannot withstand the selected settings.
Impact:
Visible marks on the fabric surface affect the visual quality and wearer comfort. Strike-through can make the fabric feel stiff or scratchy, especially in areas you need softness, like collars or inner linings.
Solution:
- Use calibrated machines with temperature and pressure settings that match the material requirements.
- AI-powered sensors can detect heat buildup and adjust the pressure to prevent the adhesive from penetrating beyond the desired layers.
- Implement predictive error detection with AI to identify issues early in production.

AI Integration in Fabric Fusing Machines: Transforming the Process
How AI Optimizes Fabric Fusing
AI adds precision and efficiency to fabric-fusing machines by automating key processes and providing real-time control over heat and pressure settings. It minimizes errors and ensures consistent quality across production runs.
Automated Decision-Making
AI-powered algorithms can analyze fabric characteristics and adjust the parameters (temperature, pressure, and speed) in real-time to ensure optimal fusing. It is beneficial when working with different fabric types in the same production line, reducing the need for manual intervention.
Predictive Error Detection
AI-powered sensors monitor for defects, such as uneven pressure or excessive heat. This proactive approach prevents strikes back and forth by making adjustments in real time.
Data Analytics and Feedback
AI enables machines to collect and analyze production data, identifying trends and bottlenecks. This feedback allows operators to fine-tune machine settings for continuous improvement, ensuring better quality and efficiency with each production batch.
Remote Monitoring and IoT Capabilities
They can connect AI-integrated fabric-fusing machines via IoT platforms for remote access and performance monitoring. Operators can track production data, receive alerts about potential issues, and initiate predictive maintenance to prevent downtime. It is valuable for small factories with limited on-site technical support.

Advantages of Using AI-Powered Fabric Fusing Machines
Precision and Quality
- AI ensures consistent control over temperature, pressure, and timing, reducing the risk of defects such as strikeback and through.
- Accurate alignment of fabric layers improves bonding strength and garment quality.
Enhanced Efficiency
- Automated AI systems streamline the fusing process, allowing for faster production cycles and increased throughput.
- Real-time adjustments minimize errors, reducing the need for rework and ensuring smoother operations.
Cost Savings
- Reduced labor costs by automating the fusing process, freeing up staff for other tasks like quality control.
- Minimizing material waste caused by defects leads to lower production costs.
Safety and Maintenance
- AI-integrated machines have predictive maintenance. It can identify potential problems, preventing breakdowns and safety.
- Automated systems eliminate manual handling of heavy fabrics and high-temperature processes, enhancing worker safety.
By integrating AI into fabric fusing machines, small garment factories and brands can overcome traditional production challenges, enhance product quality, and stay competitive in a fast-paced market.

How Small Garment Factories and Brands Can Benefit from AI-Powered Fabric Fusing
Competing with Large Brands
AI-powered fabric fusing machines allow small factories to achieve the same high-quality results as their larger counterparts without significantly increasing costs. Advanced automation ensures consistent quality, helping smaller players compete in industries like fashion, automotive, and medical supplies.
- Reduced labor dependency means they can allocate more resources to other value-added tasks, such as design or quality control.
- Faster production cycles help meet tight deadlines, which is crucial in fast-fashion and time-sensitive markets.
Affordable Access to Technology
Smaller factories often face barriers due to high upfront costs for advanced machinery. However, leasing and rental options make AI-powered fusing machines more accessible.
- Pay-per-use models allow small businesses to access advanced technology on a budget.
- Many vendors now offer low MOQ (Minimum Order Quantity) options, meaning even small-batch manufacturers can use high-tech solutions without investing in large production runs.
Flexible Production Capabilities
AI-powered machines offer customizable settings, making them ideal for both small-batch and large-scale production.
- They can make batch production adjustments on the type of fabric or product.
- Factories can cater to diverse client demands, from custom fashion collections to bulk production of standardized items like uniforms or masks.

Industry Applications of AI in Fabric Fusing
Automotive Industry
AI-powered machines handle thick fabrics like leather and polyester used in car seats, upholstery, and airbags.
- Precise heat and pressure ensure these heavy materials bond seamlessly, even under high-volume production demands.
Medical and PPE Production
Non-woven materials used for surgical masks, gowns, and other PPE require specialized fusing techniques. AI-powered machines ensure precise handling and bonding of these delicate fabrics.
- These systems are crucial during emergencies (e.g., pandemic responses) when production needs to scale up rapidly.
Outdoor Gear
AI technology helps manage sturdy and waterproof materials, such as those used for tents, backpacks, and outdoor clothing.
- Consistent tension control ensures the durability and waterproofing of outdoor gear, enhancing performance under extreme conditions.
Fashion Industry
AI-powered fabric fusing enhances the production of structured garments, such as blazers, coats, and tailored suits.
- Automated machines provide high-quality finishes while maintaining fabric integrity, meeting the demands of high-end fashion brands.

The Roadblocks to AI Adoption in Small Garment Factories in AI Adoption for Fabric Fusing
High Initial Investment
AI technology can be costly to implement. However, rental, leasing, and pay-per-use models offer solutions for small businesses.
- These options spread costs over time, reducing the financial burden.
- Factories can start with a modular approach, adopting only essential AI features and scaling up as they grow.
Learning Curve for Employees
Integrating AI-powered machines requires training and upskilling employees to operate the equipment efficiently.
- Vendors often provide training programs and technical support to smooth the integration process.
- User-friendly interfaces, like touchscreens and automated controls, also help minimize the learning curve.
Resistance to Change
Adopting new technology can meet resistance from employees and management.
- Emphasizing the long-term benefits, such as higher quality, cost savings, and increased production capacity, helps address concerns.
- Engaging employees early in the adoption process ensures smoother transitions and acceptance.

The Future of Fabric Fusing: AI, IoT, and Industry 4.0
Real-Time Data Analysis
AI-powered machines collect and analyze data from every production run, enabling immediate adjustments based on feedback.
- If a fusing defect is detected, the system automatically modifies heat and pressure settings for subsequent runs, ensuring continuous improvement.
Predictive Maintenance
AI monitors equipment performance and predicts wear and tear before it leads to machine failure.
- Scheduled maintenance minimizes downtime and ensures smooth operations.
End-to-End Automation
AI and IoT technologies allow machines to communicate with other production equipment (e.g., cutting, sewing, or finishing machines).
- This seamless integration enables end-to-end automation, streamlining the production process and improving overall efficiency.
AI-powered fabric fusing offers small garment factories and brands the tools to stay competitive, improve quality, and reduce costs. With flexible production capabilities, affordable access to technology, and the ability to handle specialized materials, these innovations are transforming the future of garment manufacturing.

Embrace AI-Powered Fabric Fusing for a Competitive Edge
AI-powered fabric-fusing machines offer numerous benefits that can significantly enhance the operational capabilities of small garment factories and brands. These machines improve the quality and efficiency of the fusing process and lead to substantial cost savings over time. They can reduce manual labor, minimize defects, and increase production capacity by automating critical aspects of fabric fusing.
As the garment industry continues to evolve, small factories and emerging brands must explore AI solutions to remain competitive. With the power of AI, your production processes can achieve higher standards of quality, faster turnaround times, and enhanced flexibility, all of which are crucial in a fast-paced market.
Partner with EverLighten
Partner with EverLighten to harness the potential of AI-powered fabric fusing and other solutions tailored to your needs. Our commitment to innovation and customer satisfaction ensures you receive the best technology and support available.
Why Choose EverLighten?
- 100% Customization: We offer tailored solutions for different fabric types and production needs.
- 100% Quality Check: Guarantee every fused garment meets the highest standards.
- Free Design Help: Get expert support with the technical aspects of fabric fusing.
- Worldwide Delivery: Serving clients globally with fast and reliable shipping.
- 24/7 Support: Assistance anytime to resolve issues quickly.
- Unlimited Revisions: We work until you are 100% satisfied.
- Low MOQ: Ideal for small brands and emerging businesses.
FAQs
- What is fabric fusing, and why is it used in garment production?
Fabric fusing involves bonding interlining to the fabric using heat and pressure. It strengthens the fabric and helps maintain its shape.
- Can AI-powered fabric fusing machines handle different fabric types?
Yes! AI systems can adjust heat and pressure settings for various fabrics, ensuring optimal results for each material.
- Are AI-powered machines a worthwhile investment for small garment businesses?
Yes, affordable options such as rentals and pay-per-use models make it accessible to small businesses. They offer significant long-term savings.
- How does AI help prevent fabric fusing defects?
AI detects potential issues in real-time and adjusts settings accordingly to maintain consistent quality, reducing the risk of defects.
- What types of garments can benefit from AI-powered fabric fusing?
AI-powered machines are versatile and suitable for applications, including structured garments, outdoor gear, automotive interiors, and medical products.