Boosting Profitability Through Smart Fabric Grouping with AI in Small Garment Factories
| Apr, 19 , 25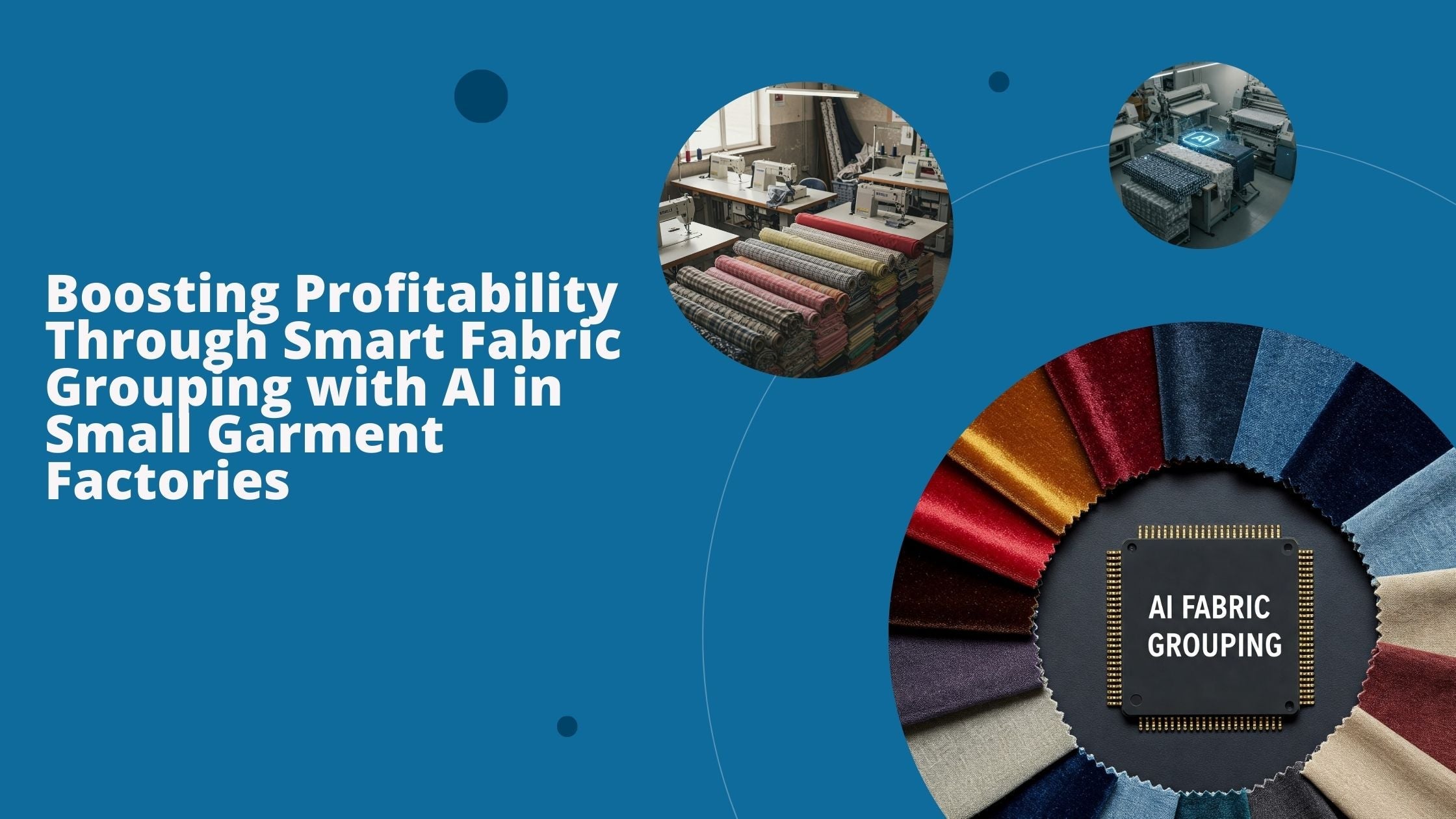
Material typically accounts for a significant part of a garment factory's running costs, ranging from 60% to 70%. Therefore, efficient fabric utilization is considered a top-tier practice and plays a vital role in achieving profitability. Maximizing the use of fabric is a highly recommended and effective strategy. It is an essential element for ensuring strong profitability. Every scrap of wasted fabric directly impacts the bottom line. This is where fabric grouping, or batching, comes into play. By categorizing fabrics based on shared characteristics, manufacturers can optimize cutting layouts, minimize waste, and improve overall material utilization while enhancing quality control.
Fabric grouping involves sorting fabric rolls based on width, tints, and shrinkage. This process ensures that fabrics with similar characteristics are used together in a single cutting lay, maximizing efficiency. While the concept is straightforward, implementing effective fabric grouping using traditional manual methods presents numerous challenges, especially for small garment factories and emerging brands. These businesses often lack the resources and sophisticated systems of significant manufacturers, relying heavily on manual processes prone to errors, inconsistencies, and inefficiencies.
These traditional methods often result in excessive fabric waste, increased labor costs, and inconsistent quality. This is where the power of Artificial Intelligence (AI) enters the picture. AI-driven solutions are revolutionizing fabric grouping by automating complex calculations, analyzing large datasets, and optimizing grouping strategies in real time. It allows small garment factories to overcome the limitations of manual methods, significantly improve fabric utilization, and ultimately boost profitability. This blog post will dive into how AI transforms fabric grouping, offering practical solutions and paving the way for a more efficient and profitable future for small garment businesses.

Understanding Fabric Grouping and Its Importance
Fabric grouping or batching is classifying fabric rolls based on shared characteristics. This systematic approach allows garment manufacturers to optimize fabric usage, minimize waste, and maintain consistent quality in the final product. The core idea is to group fabric rolls that behave similarly during cutting, sewing, and finishing, ensuring uniformity and reducing the risk of defects.
Parameters Used for Grouping:
You must consider several key parameters when grouping fabrics:
-
Shrinkage (Warp and Weft): Shrinkage refers to the dimensional change a fabric undergoes after washing or other finishing processes. It's crucial to consider both warp (lengthwise) and weft (crosswise) shrinkage. Fabrics with significantly different shrinkage rates should never be used in the same garment piece, as this can lead to distortion, puckering, and improper fit after washing. Grouping fabrics with similar warp and weft shrinkage ensures that all components of a garment shrink uniformly, maintaining its intended shape and size.
-
Width: Fabric width can vary between rolls, even within the same fabric type. If fabrics with different widths are in the cutting lay, the narrower fabric will dictate the usable width for the entire lay, leading to significant fabric waste from the wider rolls. Grouping fabrics by width allows for optimized marker planning, ensuring the maximum usable width of each fabric roll.
-
Shade: Even fabrics from the same dye lot can exhibit subtle shade variations. Using fabrics with different shades within the same garment can result in noticeable color discrepancies, especially in larger pieces or when you view different parts under varying lighting conditions. Shade grouping ensures color consistency within each garment, enhancing its visual appeal and perceived quality.
Why Accurate Fabric Grouping is Crucial:
Accurate fabric grouping is essential for several reasons:
-
Marker Planning: Markers are cutting layouts that determine how to cut to maximize yield and minimize waste. Effective marker planning relies on accurate fabric width data. Grouping fabrics by width allows markers to be created specifically for each width group, maximizing fabric utilization and reducing offcuts.
-
Cutting Plans: Cutting plans detail how to lay the fabric and cut based on the markers. Proper fabric grouping ensures correct fabric rolls for each cutting lay, preventing errors and ensuring consistent quality in the cut pieces.
-
Fabric Utilization: Fabric grouping improves fabric utilization by optimizing marker planning and cutting plans. Using fabrics with similar properties minimizes waste caused by mismatched widths, shade variations, or differential shrinkage.
-
Overall Material Utilization: Beyond just fabric, accurate grouping impacts overall material utilization by reducing the need for rework, remakes, and returns due to quality issues caused by mismatched fabrics. It leads to cost savings for materials, labor, and time.

Traditional (Manual) Fabric Grouping Methods in Small Garment Factories and Their Limitations
In many small garment factories, fabric grouping is still manual, often relying on experience, spreadsheets, and basic calculations. While the intention is sound, these manual methods are inefficient, error-prone, and struggle to handle the complexities of modern garment production.
The Manual Grouping Approach:
The typical manual approach involves the following steps:
-
Data Collection: Gathering information about incoming fabric rolls, including width, shade, and (if available) shrinkage data from supplier documents. This data is often recorded manually in spreadsheets or on paper.
-
Visual Inspection (for Shade): Trained personnel visually inspect fabric rolls to assess shade variations. Various factors, including lighting conditions and individual perception, can influence the subjective process.
-
Manual Calculations and Grouping: The Staff manually calculates and creates fabric groups based on the collected data. A common practice is dividing order quantities based on the ratio of available fabric widths or shades.
Example of Dividing Order Quantities Based on Fabric Ratios:
Let's say a small garment factory receives an order for 300 garments. They need 300 meters of fabric (assuming 1 meter per garment). They receive two groups of fabric:
-
Group 1: Width = 1.48 meters, Total length = 200 meters
-
Group 2: Width = 1.45 meters, Total length = 100 meters
The ratio of fabric length is 2:1 (Group 1: Group 2). You can split the order quantity:
-
Group 1: 200 garments
-
Group 2: 100 garments
It means separate markers and cutting lays for each group.
Problems of Manual Grouping:
While this approach seems simple, it presents several significant problems:
-
Too Many Markers: In the example above, you must create separate markers for each fabric width group. It multiplies the number of markers required if there are multiple sizes, as well as the time and complexity.
-
Too Many Lays: Each marker requires a separate cutting lay. This prolongs the spreading phase, which involves arranging fabric in layers for the cutting process. It is a significant factor in production time.
-
Too Many Cuts: You need more cutting operations, labor costs, and cutting errors.
-
Dependency on Pre-Known Fabric Ratios: The manual approach often relies on a clear understanding of the fabric ratios before starting.
-
It is limited when dealing with large orders where fabric is received in multiple deliveries over time.
-
It becomes difficult to adjust groupings as new fabric arrives.
-
It can lead to suboptimal fabric utilization and increased waste.
-
Time-Consuming and Prone to Human Error: Manual data collection, calculations, and visual inspections are time-consuming and prone to human error. Data entry, calculations, or shade-matching mistakes can lead to costly errors in cutting and garment assembly.
-
Difficulty in Handling Complex Grouping Scenarios: Real-world scenarios are rarely as simple as the example above. Small garment factories often receive fabric in multiple widths and shades with varying shrinkage rates. Manual methods struggle to handle these complex situations efficiently and optimally. It becomes nearly impossible to calculate the best grouping strategy to maximize fabric utilization while minimizing markers, lays, and cuts.

Stage / Method |
Description |
Limitations |
Consequences |
Data Collection |
Manual recording of fabric roll details (width, length, shade, shrinkage) using spreadsheets or paper |
Time-consuming, inconsistent, prone to errors |
Incorrect data can lead to faulty groupings and production waste |
Visual Shade Inspection |
Shade assessment is done by the human eye under varied lighting conditions |
Subjective, inconsistent across individuals, and shifts |
Inaccurate grouping, shade mismatches in finished garments |
Manual Grouping & Calculations |
Based on width, length, and shade, groupings are done with basic math or experience |
Cannot handle multiple variable inputs; assumes fixed, known ratios |
Too many groups created; inefficient marker planning |
Example: Grouping by Ratio |
E.g., 300 garments split: 200 garments from 1.48m width, 100 garments from 1.45m width |
Not adaptable to variable or unknown fabric deliveries |
Extra workload for marker planning and fabric laying |
Marker Creation |
Separate markers for each fabric group |
More markers are required when multiple widths/shades/sizes exist |
Increases complexity, time, and risk of layout error |
Cutting Lays |
Individual lays per marker and fabric group |
Increases spreading time and labor involvement |
Delays production, increases labor cost |
Cutting Operations |
Additional cutting setups due to more groups and lays |
More labor, higher error potential |
Increased cost and production risk |
Dependence on Known Ratios |
Relies on a fixed understanding of the available fabric at the start |
Fails when fabric comes in staggered or partial shipments |
Re-grouping is difficult; inefficient fabric usage |
Handling Complex Groupings |
Manual methods falter when dealing with combinations of width, shade, and shrinkage |
No optimization logic; not scalable |
Wastage increases, garment consistency suffers |
Overall Efficiency |
The process is highly manual and lacks adaptability |
Prone to human error, slow, and rigid |
Reduced fabric yield, higher costs, longer lead times |

AI Solutions for Fabric Grouping Challenges in Small Garment Factories
Artificial intelligence offers transformative solutions to the challenges inherent in manual fabric grouping, providing small garment factories with the tools to optimize fabric utilization, reduce costs, and improve efficiency.
-
Automated Data Collection and Analysis: One of the limitations of manual grouping is the time-consuming and error-prone process. AI automates this process by:
-
Integrating with Supplier Databases: AI systems can connect directly to supplier databases to automatically retrieve information about fabric rolls, including width, length, shade codes, and shrinkage data.
-
Automated Measurement Systems: In-house measurement systems with sensors and cameras can automatically measure fabric width and other relevant parameters as rolls are received.
-
AI-powered shade Matching: Advanced image analysis techniques can assess fabric shade. It eliminates the subjectivity of human visual inspection. AI analyzes and records the data.
-
Centralized Data Management: All collected data is stored in a centralized database accessible to the AI system and other relevant software, ensuring data integrity and consistency.
-
AI-Powered Grouping Algorithms: AI algorithms are the core of the automated grouping process. These algorithms can:
-
Consider Multiple Parameters: Unlike manual methods that often focus on a single parameter like width, AI algorithms can simultaneously consider the width, hues, shrinkage (warp and weft), order quantities, and even fabric defects to create optimal groupings.
-
Optimize for Specific Objectives: The algorithms can be programmed to optimize for different objectives, such as maximizing fabric utilization, minimizing the number of markers and lays, or minimizing shade variations within garments.
-
Use Advanced Optimization Techniques: AI employs sophisticated optimization techniques. For example, algorithms or linear programming can be used to find the best possible grouping solutions. It will be impossible to achieve manually.
-
Dynamic Grouping: This is a key advantage of AI-based grouping. Traditional methods struggle with dynamic changes in fabric availability. AI solves this by:
-
Real-Time Adjustments: As new fabric rolls arrive, the AI system automatically re-evaluates the existing groupings and adjusts as needed. It eliminates the need to pre-determine fabric ratios and allows optimal fabric utilization even with multiple deliveries and varying roll sizes.
-
Handling Large Orders and Multiple Deliveries: AI can efficiently manage complex scenarios involving large orders and multiple fabric deliveries, dynamically adjusting groupings to ensure maximum efficiency throughout the production process.
-
Integration with CAD/CAM Systems: Seamless integration between AI-powered grouping systems and CAD/CAM (Computer-Aided Design/Computer-Aided Manufacturing) systems is crucial for maximizing efficiency. This integration allows:
-
Automated Marker Generation: Based on AI-optimized fabric groupings, the system can automatically generate optimized markers for each group, minimizing fabric waste and reducing marker-making time.
-
Direct Data Transfer to Cutting Machines: You can transfer the optimized cutting plans generated by the CAD/CAM system to automated cutting machines, ensuring accurate and efficient cutting.
-
Shade Management: AI provides sophisticated shade management capabilities:
-
Shade-Wise Grouping and Cutting: AI can incorporate customer-specific shade requirements and ensure the grouping and cutting of fabrics together. It prevents shade variations within garments and meets customer expectations.
-
Shade Mapping and Tracking: AI can create shade maps for each fabric group, allowing for precise tracking of shade variations within and between rolls. It helps to manage shade consistency across different production runs.

Benefits of AI for Fabric Grouping in Small Garment Factories and Brands
Implementing AI-powered fabric grouping offers many advantages for small garment factories and brands, enabling them to optimize their operations and compete more effectively.
-
Increased Fabric Utilization and Reduced Waste are the most significant benefits. AI algorithms optimize fabric groupings and marker layouts, minimizing offcuts and maximizing the use of each fabric roll. It translates directly to substantial cost savings on raw materials and contributes to more sustainable manufacturing practices.
-
Reduced Number of Markers, Lays, and Cuts: AI minimizes the need for multiple markers and cutting lays by creating optimal groupings. Fewer layers mean less spreading time, fewer cuts reduce labor costs and the potential for cutting errors. This streamlined process significantly increases overall production efficiency.
-
Improved Quality Control: AI ensures consistent fabric properties within each group, leading to more uniform and predictable results in cutting, sewing, and finishing. It reduces the risk of defects caused by mismatched fabrics, improving the overall quality and consistency of the finished garments. It also minimizes the need for costly rework and returns.
-
Faster and More Accurate Grouping: Automating the data collection, analysis, and grouping process with AI significantly reduces the time required for fabric management. It also eliminates the human error associated with manual methods, ensuring greater accuracy and consistency in grouping decisions. It frees up valuable time for staff to focus on other critical tasks.
-
Ability to Handle Complex Grouping Scenarios: AI can efficiently manage complex scenarios involving multiple fabric widths, shades, shrinkage rates, and large orders with multiple deliveries. This level of complexity is challenging to handle manually, making AI an invaluable tool for managing complex fabric inventories and production schedules.
-
Improved Profitability and Competitiveness: The above benefits contribute to improved profitability and competitiveness. A healthier bottom line is achieved through a combination of factors, including less material waste, reduced labor costs, greater efficiency, and improved product quality. It allows small garment factories and brands to compete more effectively with prominent manufacturers, offering high-quality products at competitive prices.

AI-Powered Fabric Grouping in Small Garment Factories: Solutions & Benefits
AI Solution Area |
How It Works |
Challenges Solved |
Key Benefits |
Automated Data Collection & Analysis |
- Connects to supplier databases for auto-import of width, shade, shrinkage, etc. - In-house sensors measure incoming roll specs - AI analyzes and records data |
Eliminates manual data entry and subjective visual inspections |
Accurate, real-time data collection; reduced human error |
AI-Powered Shade Matching |
- Uses image analysis to assess fabric shades - Standardizes shade recognition |
Removes subjectivity and lighting bias in human inspection |
Consistent shade classification and grouping |
Centralized Data Management |
- All fabric data is stored in one integrated system accessible by all relevant tools |
Avoids scattered spreadsheets and inconsistent records |
Unified data source for faster, smarter decisions |
AI Grouping Algorithms |
- Simultaneously considers width, shrinkage, shades, defects, etc. - Optimizes for goals like fewer markers, better shade uniformity, or max utilization |
Manual grouping struggles with multiple parameters and optimal trade-offs |
Data-driven grouping reduces waste and complexity |
Advanced Optimization Techniques |
- Uses AI models like linear programming or genetic algorithms |
Manual methods can't compute optimal solutions across complex input sets |
Smarter grouping, higher efficiency, and lower cost |
Dynamic Grouping |
- AI adjusts groupings in real-time as new fabric rolls arrive |
The manual approach is rigid and fails with staggered deliveries |
Flexibility with deliveries, better fabric utilization, and faster decision-making |
Integration with CAD/CAM |
- Auto-generates markers from AI groupings - Transfers data to automated cutters |
Manual systems require separate, error-prone steps |
Speeds up cutting, reduces manual labor, ensures marker accuracy |
Shade Management Tools |
- Groups and cuts based on exact shade - Maps and tracks shade variations across rolls |
Human shade grouping is imprecise and inconsistent |
Higher garment consistency and customer satisfaction |
Complex Group Handling |
- Handles multiple shades, widths, shrinkage rates, and staggered deliveries |
Manual systems break down with complexity |
Enables scalable, efficient grouping for large/complex orders |

Smart Fabric Grouping: A Key to Profitability in the Garment Industry
Effective fabric management is crucial for success in the garment industry, and fabric grouping is vital in optimizing fabric utilization and controlling costs. While traditional manual methods present numerous challenges, AI-powered solutions offer a powerful way to overcome these limitations. By automating data collection, optimizing grouping strategies, and integrating with existing systems, AI empowers small garment factories and brands to reduce waste, improve efficiency, and boost profitability. Embracing AI for fabric grouping is not just an upgrade; it's a strategic investment in the future of your business.
Eager to fundamentally change how you manage fabric and unlock your business's full profit potential?
At EverLighten, we're dedicated to helping businesses of all sizes thrive in the competitive garment industry. We understand the importance of efficient fabric utilization and offer comprehensive manufacturing solutions tailored to your needs. We provide:
-
100% Customization: We tailor every aspect of your garment production, from fabric selection and design to labeling and packaging.
-
100% Quality Check: Rigorous quality control at every production stage ensures that your garments meet the highest standards.
-
Free Design Help: Our expert design team will bring your creative vision to life.
-
Worldwide Delivery: We offer reliable worldwide shipping to deliver your finished products wherever you are.
-
24/7 Support: Our dedicated support team is available around the clock to answer your questions and provide assistance.
-
Unlimited Revisions: We guarantee your total satisfaction with the final product and will make as many changes as needed until you are pleased.
-
Low MOQ: We cater to businesses of all sizes with low minimum order quantities, making custom garment production accessible to everyone.
Connect with EverLighten today to discuss your garment manufacturing needs and discover how we can help you optimize your fabric utilization and boost your profitability. Let us be your trusted partner in creating high-quality, cost-effective garments.
FAQs
Q: How does AI-powered fabric grouping differ from traditional methods?
Traditional methods rely on manual data collection, calculations, and visual inspections, which are time-consuming, error-prone, and challenging in complex scenarios. AI automates these processes, using advanced algorithms to optimize groupings based on multiple parameters.
Q: Is AI fabric grouping only beneficial for large factories?
No, AI solutions are becoming increasingly accessible and scalable. It makes it beneficial for small garment factories. Reduced waste and increased efficiency are valuable for small factories and brands.
Q: What data does AI use for fabric grouping?
AI systems can use various data points, including fabric width, shade codes, shrinkage rates (warp and weft), order quantities, and fabric defect information. This data can be collected automatically from supplier databases, in-house measurements, and other sources.
Q: How does AI ensure shade consistency within garments?
AI can use advanced image analysis to assess fabric shade and create shade maps for each group. It ensures that fabrics with similar shades are used together in the same garment, preventing noticeable color discrepancies. AI can also incorporate shade-wise shipping requirements.
Q: Does implementing AI require significant changes to existing factory infrastructure?
The level of infrastructure changes depends on the specific AI solution implemented. Some solutions can integrate with existing CAD/CAM systems with minimal disruption, while others may require new hardware or software. However, the long-term cost savings and efficiency gains often justify the initial investment.