Stop Guessing, Start Knowing: AI's Smart Approach to Apparel T&A Planning in Small Garment Factories
| Apr, 02 , 25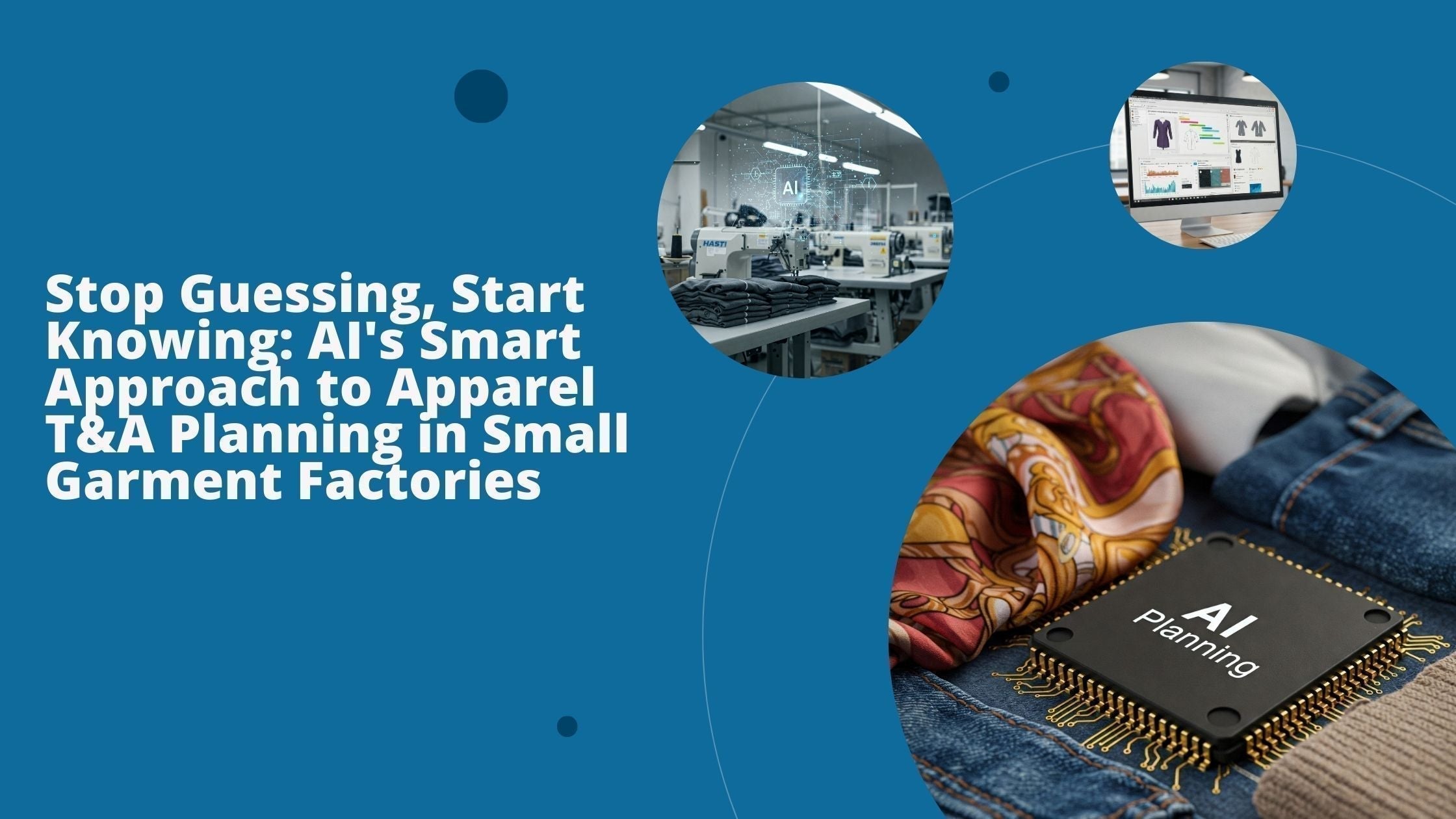
The Evolving Landscape of Apparel Production Planning
In the fast-paced world of apparel manufacturing, meeting deadlines is paramount. A well-executed Time and Action (T&A) plan is the backbone of any successful production run, outlining every step from initial order placement to final shipment. These plans are crucial for coordinating various departments, managing supplier relationships, and ensuring on-time delivery.
Traditionally, T&A planning has relied heavily on spreadsheets – a familiar tool that often falls short in dealing with the complexities of modern apparel production.
Spreadsheets offer a basic framework for tracking tasks and deadlines but struggle to manage the intricate web of dependencies between different production activities. Estimating lead times becomes a guessing game based on experience, often leading to inaccuracies and costly delays. Real-time visibility into project progress is limited, and team communication can become fragmented. In short, while widely used, the spreadsheet approach is prone to inefficiency and errors.
But what if you could move beyond guesswork and start knowing? Artificial intelligence (AI) is transforming apparel production planning, offering intelligent solutions that address the inherent limitations of traditional methods. AI-powered T&A planning provides accurate lead time predictions, intelligent dependency management, real-time project tracking, enhanced communication, and proactive risk mitigation.
This blog post will explore how AI has revolutionized apparel production planning in small garment factories. We will delve into the specific ways AI is addressing the challenges of traditional T&A planning, empowering businesses to achieve greater efficiency, accuracy, and profitability. We will show you how to stop guessing and start knowing using the power of AI. But let us understand the

Traditional T&A Planning in Small Garment Factories: A Manual and Inefficient Process
Time and Action (T&A) planning in small garment factories relies heavily on manual methods, primarily spreadsheets. While seemingly simple, this approach presents significant challenges in today's dynamic production environment.
The Spreadsheet Method:
The traditional spreadsheet-based T&A plan typically involves:
-
Listing Actions: A column lists all the necessary steps in the production process, from fabric sourcing and approval to cutting, sewing, finishing, and shipping.
-
Estimated Completion Dates: Another column contains the estimated completion date for each action, often based on historical data, experience, or simply a best guess.
-
Actual Completion Dates: They record the completion date in a separate column once an action is complete.
This basic structure allows for some tracking in small garment factories, but it quickly becomes cumbersome and inefficient for complex orders with numerous interdependencies.
Limitations and Pain Points AI Can Solve:
Here's a breakdown of the key limitations of manual T&A planning in small garment factories and how AI can provide solutions:
-
Inaccurate Lead Time Estimation: Manual estimation is a significant source of inaccuracy. Relying on past data or gut feelings doesn't account for variations in supplier lead times, factory capacity, or unexpected delays. It often leads to missed deadlines and rushed production, increasing costs and potentially compromising quality. AI can solve this by analyzing historical data, supplier performance, and external factors (weather or global events) to provide more accurate and dynamic lead time predictions for small garment factories.
-
Difficulty Managing Complex Dependencies: Apparel production involves complex interconnected activities. For example, cutting cannot begin until the fabric is received and approved. Spreadsheets struggle to visualize and manage these dependencies, making it difficult to understand the impact of delays in one area on the rest of the production process. AI-powered T&A systems can automatically map these dependencies. It can create a clear visual representation of the project timeline and highlight critical paths.
-
Lack of Real-Time Visibility and Tracking: Manually updating spreadsheets is time-consuming and prone to errors. It provides only a snapshot of the project for the update, offering little to no real-time insight into progress. This lack of visibility makes it difficult to identify and address potential delays. AI-powered systems provide real-time project progress, automatically updating the T&A plan as activities are completed. It allows for immediate identification of bottlenecks and proactive intervention.
-
Inefficient Communication and Collaboration: Spreadsheets are not ideal for collaboration. Sharing and updating them can be cumbersome, leading to version control issues, miscommunication, and delays. AI-powered platforms offer centralized data access and automated reporting, facilitating seamless communication and collaboration among teams, suppliers, and stakeholders.
-
Inability to Proactively Identify and Mitigate Risks: Manual methods offer limited capacity to anticipate potential problems. Delays in one area can affect the entire production schedule, and spreadsheets impart little help with these risks. AI can analyze data to identify potential perils and bottlenecks early on, such as supplier delays or capacity constraints. It can even suggest mitigation strategies and optimize resource allocation to minimize the impact of these risks.

AI-Powered T&A Planning in Small Garment Factories: A Smart Solution
Artificial intelligence offers a suite of tools to address the shortcomings of traditional T&A planning. Here's how AI is transforming the process:
A. AI-Driven Lead Time Prediction:
-
Analyzing Data for Accurate Predictions: AI algorithms can analyze vast amounts of historical data, including past order completion times, supplier lead times, factory capacity, material availability, and external factors like weather patterns or global events. By identifying patterns and correlations in this data, AI can predict lead times better than manual estimation.
-
Improving Planning Accuracy and Reducing Delays: Accurate lead time predictions are essential for creating realistic T&A plans. By minimizing the guesswork involved in manual estimation, AI helps prevent overly optimistic or pessimistic schedules, reducing the risk of missed deadlines and production bottlenecks. It also allows for more accurate quoting and better management of customer expectations.
B. Intelligent Dependency Management:
-
Automating Dependency Mapping: AI-powered platforms can automatically map the complex interdependencies between production activities. For example, the system can understand that cutting cannot begin until the fabric is received and approved and that sewing cannot start until cutting is complete. This automated mapping eliminates manual tracking and reduces the risk of errors.
-
Improving Project Visualization and Identifying Critical Paths: AI-powered platforms make it easier to understand the project flow and identify the critical path by visually representing the dependencies between activities. It allows project managers to focus on the most vital tasks and prevent delays that could impact the project timeline.
C. Real-Time Project Tracking and Monitoring:
-
Providing Real-Time Visibility: AI-powered systems give real-time visibility into project progress. The system automatically updates the T&A plan, providing an accurate and up-to-the-minute view of the project's status.
-
Benefits of Automated Alerts and Notifications: The system can send automated alerts and notifications to relevant stakeholders when deadlines are approaching, activities are late, or potential bottlenecks. It enables proactive intervention and prevents tiny issues from escalating into major problems.
D. Enhanced Communication and Collaboration:
-
Facilitating Seamless Communication: AI-powered platforms provide a centralized hub for all project-related information, facilitating seamless communication and collaboration among different teams, suppliers, and stakeholders.
-
Benefits of Centralized Data and Automated Reporting: Centralized data eliminates the need for multiple spreadsheets and reduces the risk of version control issues. Automated reporting regularly updates stakeholders on project progress, keeping everyone informed and aligned.
E. Proactive Risk Management and Mitigation:
-
Identifying Potential Risks and Bottlenecks: AI can analyze data from various sources to identify potential risks and bottlenecks early on. For example, the system might identify a delay in fabric delivery due to supplier issues or predict a bottleneck in the sewing department due to capacity constraints.
-
Suggesting Mitigation Strategies and Optimizing Resource Allocation: Based on its analysis, the AI system can suggest mitigation strategies, such as finding alternative suppliers or reallocating resources to address potential bottlenecks. This proactive approach helps minimize the impact of unforeseen events and keeps projects on track.

Benefits of AI-Driven T&A Planning for Small Garment Factories
Implementing AI-driven Time and Action (T&A) planning offers many benefits for small garment factories, enabling them to operate more efficiently, effectively, and profitably.
-
Increased Efficiency and Productivity:
-
Automation of Tasks: AI automates many time-consuming manual tasks associated with T&A planning, such as data entry, dependency mapping, and report generation. It frees up valuable time for employees to focus on more strategic activities.
-
Improved Resource Allocation: By accurately predicting lead times and identifying potential bottlenecks, AI helps optimize resource allocation. It means assigning the right people and equipment to the right tasks at the right time, maximizing productivity, and minimizing downtime.
-
Reduced Lead Times and On-Time Delivery:
-
Accurate Lead Time Prediction: AI's ability to analyze historical data and other relevant factors leads to more accurate lead time predictions. It allows for realistic scheduling and reduces the risk of missed deadlines.
-
Proactive Risk Management: AI enables proactive intervention, preventing tiny issues from escalating into major problems that could impact the project timeline and lead to late deliveries.
-
Improved Accuracy and Reduced Errors:
-
Data-Driven Decision-Making: AI replaces subjective judgment with data-driven insights, minimizing the risk of human error in estimations and planning.
-
Automated Tracking: Automated project tracking progress reduces the need for manual updates and eliminates the risk of data entry errors.
-
Enhanced Communication and Collaboration:
-
Centralized Data: AI-powered platforms provide a central repository for all project-related information, ensuring everyone involved can access the same up-to-date data. It eliminates confusion and miscommunication caused by disparate spreadsheets or email threads.
-
Automated Reporting: Automated reporting tools provide regular updates on project progress to all stakeholders, keeping everyone informed and aligned. It improves transparency and facilitates better communication.
-
Better Risk Management and Mitigation:
-
Proactive Identification of Potential Delays: AI algorithms can analyze various data points to identify potential risks and bottlenecks early in the production process, such as supplier delays, capacity constraints, or material shortages.
-
Proactive Mitigation of Potential Delays: The system can even suggest mitigation strategies, such as finding alternative suppliers, adjusting production schedules, or reallocating resources, to minimize the impact of potential delays. This proactive approach helps keep projects on track and avoids costly disruptions.

Aspect |
Traditional Challenges |
AI-Powered Solutions |
Key Benefits / Outcomes |
A. Lead Time Prediction |
- Manual estimation relies on historical data and guesswork. - Limited ability to account for external factors like weather, supplier delays, or capacity constraints. |
- AI algorithms analyze vast amounts of historical and real-time data (order completion times, supplier lead times, material availability, etc.). - Predictive models forecast accurate lead times. |
- Improved planning accuracy. - Reduced production delays and bottlenecks. - More reliable quoting and better management of customer expectations. |
B. Intelligent Dependency Management |
- Manual mapping of interdependencies between production activities is error-prone and time-consuming. - Difficulty identifying critical paths and potential delays. |
- AI platforms automatically map production dependencies (e.g., fabric delivery to cutting, cutting to sewing). - Visual representations highlight critical paths and bottlenecks. |
- Enhanced project visualization. - Focus on vital tasks to prevent delays. - Reduced risk of miscommunication and scheduling errors. |
C. Real-Time Project Tracking |
- Manual tracking methods provide delayed and often inaccurate updates. - Lack of real-time visibility delays corrective actions. |
- AI-powered systems continuously monitor project progress and update T&A plans in real time. - Automated alerts notify stakeholders when deadlines are at risk. |
- Proactive intervention minimizes disruptions. - Timely adjustments ensure on-time delivery. - Increased overall operational efficiency. |
D. Enhanced Communication & Collaboration |
- Reliance on disparate spreadsheets and manual reports leads to miscommunication. - Inconsistent data sharing among teams and suppliers. |
- Centralized AI platforms consolidate all project data into one accessible hub. - Automated reporting and alerts keep everyone informed and aligned across departments and with suppliers. |
- Streamlined communication and data transparency. - Improved collaboration and decision-making. - Reduced confusion and errors due to consistent, up-to-date information. |
E. Proactive Risk Management |
- Traditional methods struggle to identify potential delays or risks early on. - Reactive strategies result in costly disruptions and rushed adjustments. |
- AI analyzes data from multiple sources to detect early warning signs of potential delays (e.g., supplier issues, capacity constraints). - Suggests mitigation strategies and resource reallocation to address risks proactively. |
- Early identification and resolution of issues. - Minimized impact of unforeseen events. - Reduced production downtime and improved project reliability. |

Implementing AI in Your T&A Planning Process in Small Garment Factories
Integrating AI into your T&A planning process doesn't require overhauling your existing systems. Several accessible options and practical steps can help small garment factories adopt this transformative technology.
Accessing AI-Powered T&A Planning Tools and Platforms:
-
Cloud-Based T&A Software with AI Features: Many cloud-based project management and production planning software solutions incorporate AI features. These platforms often offer subscription-based pricing, making them accessible to small garment factories. Look for features like AI-driven lead time prediction, automated dependency mapping, and real-time project tracking.
-
Specialized AI-Powered T&A Platforms: Some companies are developing specialized AI-powered platforms for the apparel industry. These platforms may offer more advanced features, such as predictive analytics for risk management and optimized resource allocation.
-
Integration with Existing ERP/MRP Systems: If your small garment factory already uses an Enterprise Resource Planning (ERP) or Material Requirements Planning (MRP) system, explore whether it offers integrations with AI-powered T&A tools. It can streamline data flow and minimize disruption to existing workflows.
-
Consultancy and Custom Solutions: For businesses with specific needs or complex workflows, consulting with AI experts or software developers may be an option. They can help develop custom AI solutions tailored to your factory's requirements.
Practical Tips for Integrating AI into Existing Workflows:
-
Start with a Pilot Project: Don't try to implement AI across all your production processes. Start with a small pilot project to test the effectiveness of the chosen AI tool and identify any potential challenges.
-
Focus on a Specific Pain Point: Identify the significant pain point in your current T&A planning process, such as inaccurate lead time estimation or difficulty managing dependencies. Focus on implementing an AI solution that directly addresses this specific issue.
-
Data Preparation and Migration: Ensure your existing data (historical order data, supplier information, etc.) is clean, organized, and in a format you can import into the AI system.
-
Training and Onboarding: Provide adequate training and onboarding for your team on how to use the new AI-powered tools. Emphasize the benefits of the technology and address any concerns or resistance to change.
-
Phased Rollout: Implement the AI solution in phases, starting with a small group of users or a specific department. It allows for adjustments and fine-tuning before a full-scale rollout.
-
Combine AI with Human Expertise: AI is a powerful tool but not a replacement for human expertise. Encourage your team to combine AI-driven insights with their knowledge and experience.
-
Monitor and Evaluate Performance: Continuously monitor the performance and evaluate its impact on your T&A planning process. Track key metrics such as on-time delivery rates, lead time accuracy, and production efficiency.
-
Iterate and Improve: Based on the performance data and feedback, iterate and improve your implementation strategy. The field of AI is constantly evolving, so it's vital to stay up-to-date on the latest advancements and explore new ways to leverage the technology.

Embracing the Future of Apparel Production with AI-Powered T&A Planning
The future of apparel production lies in intelligent planning. By embracing AI-powered Time and Action planning, small garment factories can move beyond the limitations of manual methods and achieve greater efficiency, accuracy, and profitability. AI offers a potent suite of tools to predict lead times, manage complex dependencies, track progress in real time, enhance communication, and mitigate risks, ultimately leading to improved on-time delivery and greater customer satisfaction.
Ready to transform your T&A planning process and take your apparel production to the next level? EverLighten is here to support you. We offer expertise in custom apparel manufacturing and can help you leverage the latest technologies to streamline your business.
Why Partner with EverLighten?
-
100% Customization: We offer complete customization for your apparel production, allowing you to create unique, high-quality garments.
-
100% Quality Check: We maintain rigorous quality control standards throughout production, ensuring your garments meet your specifications.
-
Free Design Help: Our experienced design team can assist you with everything from garment design to artwork preparation and fabric selection.
-
Worldwide Delivery: We offer worldwide shipping, allowing you to reach customers globally.
-
24/7 Support: Our dedicated customer support team is available around the clock to answer your questions and provide assistance.
-
Unlimited Revisions: We offer unlimited revisions during the sampling phase to ensure your complete satisfaction.
-
Low MOQs: We offer flexible minimum order quantities to accommodate businesses of all sizes.
Contact us today for a free quote, and let us help you optimize your apparel brand.
FAQs:
How does AI improve lead time estimation in T&A planning?
AI analyzes historical data, supplier performance, and other relevant factors to identify patterns and correlations, providing more accurate and dynamic lead time predictions than manual estimations.
What are the benefits of real-time project tracking in AI-powered T&A systems?
Real-time tracking provides up-to-the-minute visibility into project progress, allowing for immediate identification of bottlenecks and proactive intervention to prevent delays. Automated alerts and notifications further enhance this proactive approach.
How does AI enhance communication and collaboration in apparel production?
AI-powered platforms provide a centralized hub for all project-related information, facilitating seamless communication and collaboration among various teams, suppliers, and stakeholders. Automated reporting ensures that everyone stays informed and aligned.
Can AI help small garment factories manage risks in production?
Yes. AI can analyze data to identify potential risks and bottlenecks early on, such as supplier delays or capacity constraints. It can even suggest mitigation strategies and optimize resource allocation to minimize the impact of these risks.
How can small garment factories access AI-powered T&A planning tools?
Small businesses can access AI tools through cloud-based T&A software with AI features, specialized AI-powered T&A platforms, integrations with existing ERP/MRP systems, or consulting with AI experts for custom solutions. Starting with a pilot project and focusing on specific pain points are effective implementation strategies.